Fourmark Manufacturing
- More production
Fourmark Manufacturing
Fourmark is a highly innovative contract moulding company that produces over a billion parts per year for the world’s most trusted brands. The company is a Global PAC Award winner for introducing the world’s first compostable bio-resin coffee pods. Fourmark is also known for speed, quality, accuracy and dependability. They run 15 fully robotic systems and 22 injection moulding machines, with a track record of 94% uptime.
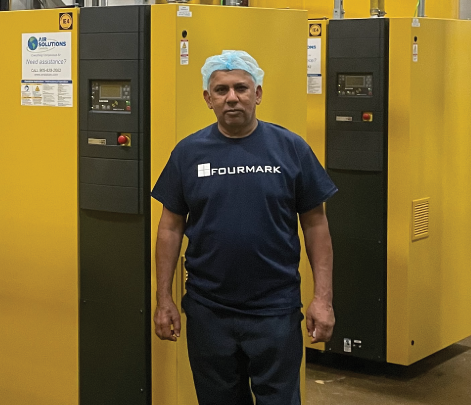
Air quality, reliability, and backup redundancy
Fourmark’s existing compressed air system included two 75KW (100-hp) water-cooled compressors:
- Atlas Copco GA 75VSD (449 cfm/188 psig)
- CompAir L75S (444 cfm/132 psig)
- Average consumption: 450 cfm
- Specific power consumption: 21.18 KW/100 cfm
These compressors were creating reliability concerns and were unable to provide service and emergency backup redundancy. One compressor could not cope alone and the second ran for very short periods of time to “top up” the system shortfall. The legacy compressors and associated purification equipment (filters and dryers), were unable to meet Fourmark’s customer air quality specifications. Subsequently, they were in the market for an oil-free compressor system solution.
Proper needs assessment and right-sized equipment
We conducted a discovery call at no charge to assess the site condition and future compressed air objectives. A benchmark was created by conducting a third-party breathing air test. The results confirmed that oil carryover, odour and vapour were the areas that needed improvement. Oil-free machines were not in fact necessary. Instead, correctly sized oil-injected compressors with 3-stage filtration and a new air dryer would be able to meet and exceed the required compressed air quality class. This significantly reduced the overall capital cost of the proposal.
Upon completion of an Air Demand Analysis (ADA) study, our Kaeser engineer recommended the installation of three fixed-speed CSD75 compressors, two to cover the actual CFM requirement and one as a redundant service and emergency backup.
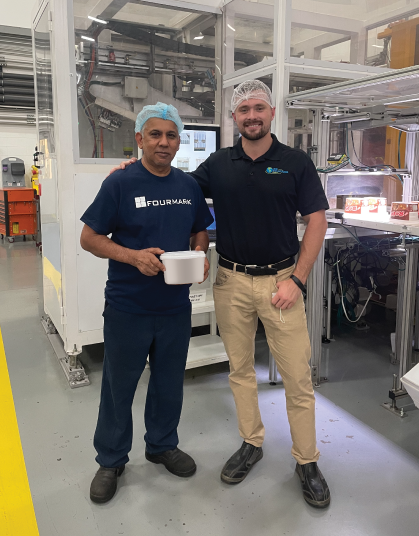
Major savings due to improvements in energy efficiency
- The new Kaeser system is now consuming 850,056.968 kWh, reducing the plant’s electricity consumption by 90,565.112 kWh.
- Total available output capacity was increased from 957.8 cfm to 1,035 cfm, allowing for future production growth.
- Specific power was reduced from $21.18 to $17.18 kW/100 cfm.
- Total estimated annual energy costs were reduced from $122,280 to $94,407.
Almost $100k reduction in capital costs achieved through proper needs assessment
With proper due diligence with respect to Fourmark’s air quality needs, we were able to reduce capital costs by $97,981 before even beginning the project (the price difference between oil injected and oil-free).
The new Kaeser compressed airsystem will achieve annual energy savings of 90,565.112 kWh or $27,873.
We were also able to help Fourmark secure an energy rebate of $9,800.
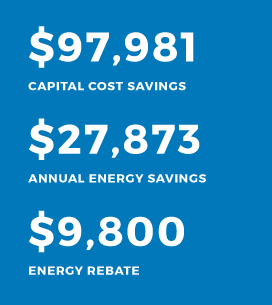
“Kaeser Compressors and Air Solutions Canada came highly recommended by other packaging manufacturers.
It was a pleasure working with their highly trained technician throughout the project, and installation was done in a timely and professional manner.
As a food packaging manufacturer, we require clean air. The filtration system they installed meets our air quality requirements, with significant savings compared to filtration we have used in the past.
We are very happy with the performance of the system, along with Air Solutions’ preventative maintenance plan, which eliminates potential problems with the compressor. Response to service calls has been fast and professional.”
Hemant Rambarack
Maintenance Manager
Fourmark Manufacturing
Discover your opportunities for savings!
Contact Air Solutions Canada to arrange your own comprehensive Air Demand Analysis, or a complimentary leak detection demonstration.
Just give us a call at 289-902-3576 or use the form above to get in touch.
Related products
The ultimate guide on rightsizing your compressed air system
Choosing the right compressed air system is crucial to minimize the total cost of ownership. How do you calculate the air demand in flow rate (CFM) and pressure (PSIG), what's the power requirement (V), and how does that translate in a compressed air system with one or more compressors (hp)?
Download our Comprehensive Guide for Choosing the Right Compressor Size!