Collective Arts Brewing
- More production
Collective Arts Brewing
Collective Arts Brewing is a craft brewery in Hamilton, Ontario, Canada, founded by Matt Johnston and Bob Russell. It is a grassroots brewery whose mandate is to combine "the craft of brewing with the inspired talents of emerging and seasoned artists, musicians, photographers and filmmakers."
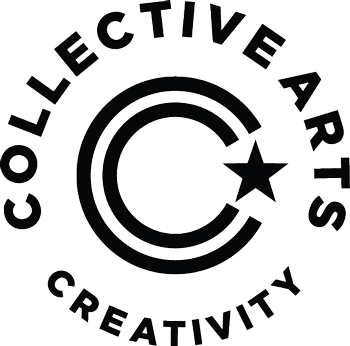
Unnecessary run time, aging equipment, & excessive heat
Since their inception in 2014, Collective Arts had been using a 75hp air-cooled Kaeser CSD75 compressor that they inherited from the previous tenant. They approached Air Solutions Canada for service and advice. During a free discovery call, Air Solutions Canada identified several opportunities for improvement with the existing compressed air installation:
- The 75hp Kaeser compressor was operating in its “unloaded” mode for many more hours than it was “loaded.” This meant that it was running for no reason and way more than necessary. The time it was actually compressing air was almost negligible. Subsequently, energy costs and power consumption were extremely high and wasteful. All of these signs indicated that a 75 hp machine was oversized, as it was only “loaded” 20% of the time.
- The air dryer was reaching the end of its useful life and showed signs of internal corrosion and high differential pressure drop. The R22 refrigerant was not in line with current environmental and Montreal protocols.
- The compressed air equipment was located in the same room as the boilers. This is a common occurrence in many manufacturing facilities, which typically results in excessive operating temperatures, particularly during the summer months. At Collective Arts, our concern was that these unusually high operating temperatures would increase the downstream oil/water condensate levels and overload the clean air treatment. Experience would also suggest the likelihood of a potential premature failure of the air compressor air end assembly.
Demand-side investigation, leak detection, & air demand analysis
We began with a demand-side investigation and leak detection study to fully understand how the system was currently using air and whether there were any obvious efficiency and repair opportunities. The leak detection study discovered 11 cfm of leaks (15% of their average air demand of 75 cfm). Most leaks were joints or fittings that could be easily repaired by their pipefitter.
We next conducted an Air Demand Analysis. This continuous study measures the compressed air generation, consumption, pressure and electricity usage every four minutes to determine the actual compressed air performance over a representative work week. The results were as follows:
- Demand was overly variable: maximum demand was 263 cfm but average demand was only 75 cfm.
- Specific energy consumption was 53.27 kW/100 cfm. (For this size and type of system, we expect to see specific power levels in the mid to low twenties).
Two compressors are better than one
Kaeser’s engineer concluded that an 18-month ROI could be achieved with new equipment, heating, and cooling solutions for summer and winter months, and 5-year Kaeser “bumper-to-bumper” warranty coverage.
Typically, a single variable-speed compressor is the recommended solution for a plant with this kind of erratic demand and consumption profile; however, Kaeser engineers demonstrated that this was not the most efficient or cost effective solution for this case. Instead they recommended two 30hp fixed-speed compressors.
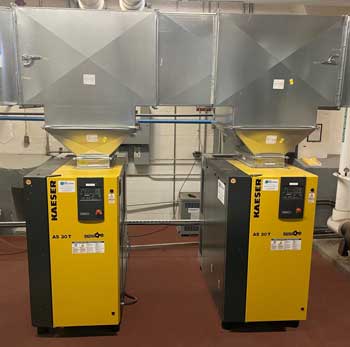
Kaeser’s KESS study, (Kaeser Energy System Study), predicted a specific energy consumption of only 22.12 kW/100cfm based on the brewery’s air consumption profile. In addition to energy savings, having two compressors also ensures that pneumatic energy is available when one compressor needs service. In addition, fixed-speed compressors have a significantly lower capital cost than variable-speed drive compressors to begin with, and have fewer moving parts. Fixed-speed machines can also better tolerate brown outs and dirty power.
The KESS report also confirmed that adding air storage would help to sustain constant system pressure and reduce the load/idle demands on the air compressor.
The existing 400-gallon air receiver was deemed to be undersized, based on “best practice” storage recommendations (3 to 6 gallons per total cfm output of the compressors). To address this, an additional 660 gallons of air storage was added to the existing 400 gallons. With the 1060 gallons of storage in place, the new ratio was 3.75 gal to 1 cfm.
Finally, we recommended and executed the design and installation of fresh air intake and heat recovery ductwork. The ductwork is designed to eject heat from the compressor room during summer months and direct the hot air discharge into the building for space heating in winter. With this added control, the efficiency of the compressed air system was greatly improved. Controlling the air temperature in the compressor room helps the system deliver dry compressed air to the facility in a reliable manner, while extending the service life of the compressed air equipment. More importantly, heat recovery savings were improved by virtue of the air compressor hot air discharge being directed into the warehouse. The increased ambient temperature in this area means that natural gas heating was subsequently reduced.
ROI achieved in just 18 months
The total cost of the equipment installed for this project will be recovered in less than 18 months, when one considers efficiency and maintenance savings associated with the new equipment. In addition to replacing equipment that was nearing the end of its useful life, the customer now has some redundancy in their compressed air system. With two independent compressors, each with integrated refrigerated air dryers, the facility will have enough compressed air to operate most of their production, even if one of the compressors is down for service or maintenance.
“We couldn’t be happier with the level of expertise and service provided by Air Solutions Canada and Kaeser throughout this project. The resulting cost savings and performance are great, and the built-in redundancy gives us peace of mind.”
David Muldoon
Engineering Manager & Process Specialist
Collective Arts Brewing
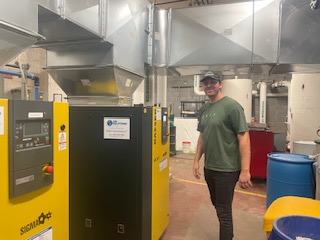
Discover your opportunities for savings!
Contact Air Solutions Canada to arrange your own comprehensive Air Demand Analysis, or a complimentary leak detection demonstration.
Just give us a call at 289-902-3576 or use the form above to get in touch.
See what our customers are saying about us!
See All ReviewsRelated products
The ultimate guide on rightsizing your compressed air system
Choosing the right compressed air system is crucial to minimize the total cost of ownership. How do you calculate the air demand in flow rate (CFM) and pressure (PSIG), what's the power requirement (V), and how does that translate in a compressed air system with one or more compressors (hp)?
Download our Comprehensive Guide for Choosing the Right Compressor Size!