Metal Packaging Company
- More production
Metal packaging company
This global metal packaging client produces all types of metal beverage and food cans, metal closures, and specialty packaging. They approached Air Solutions Canada to assist with one of their GTA facilities.
An outdated, inefficient system
In 2021, after completing a plant overhaul that shifted the production focus to strictly beverage cans, this company completed an analysis of the plant’s compressed air system. Here is the breakdown of the legacy equipment that was in use:
- Four 300hp and two 350hp modulating water-cooled compressors.
- Four 20hp air blast aftercoolers to improve compressed air quality (in particular, liquid oil and dew point).
- Four undersized, water-cooled refrigerated air dryers.
- Two large coalescing filters, which struggled to clean the compressed air, at generation, of unwanted oil contamination.
- 25 additional point-of-use filter housings to meet the required air quality at production machinery. Air Solutions Canada worked with the client to identify the following project objectives:
- Complete replacement of the legacy system.
- Reduction of the compressed air system footprint.
- Identification and repair of leaks.
- Elimination of cooling water.
- Heat of compression reclaim.
- Reduction of repair and maintenance costs.
- Introduction of redundant backup.
- Remote monitoring.
- Stable system pressure.
- ISO compressed air quality class 1:4:1.
- Improved uptime and reliability.
- Applying for and winning incentives.
A complete overhaul
- We began by detecting and repairing compressed air leaks. Cfm demand was immediately reduced by almost 600cfm.
- We installed three 250hp air-cooled Kaeser ESD250 compressors and three 300hp Kaeser ESD300 compressors, providing total flexibility and redundant backup to cover emergency and service downtimes.
- We introduced four new, air-cooled, air dryers, correctly sized to cope with the high ambient temperatures and humidity in Ontario during the summer, ensuring a 3°C pressure dew point.
- New high efficiency coalescing oil-removal filters contribute to an increased compressed air ISO quality class.
- During a site visit, we noticed that the plant used heated water for their can rinse process. We offered to factory fit the compressors with plate-and-frame heat exchangers to preheat the process water and reduce their heating costs. Before it is heated, the cold water used in this process exchanges with the compressors’ hot lubricating oil system to enhance the cooling process. These exchangers generate approximately 1,440,000 Btu/hr in heating and cooling energy.
- All equipment is orchestrated by a Sigma Air Manager master controller. The SAM 4.0-8, is monitored remotely by Air Solutions Canada, providing comprehensive data, including system pressure and flow patterns, maintenance notifications, individual compressor motor energy, and even overall system energy and maintenance costs.
Major improvements in energy efficiency
Air Solutions Canada fulfilled the client’s entire wishlist “in house,” with nothing being subcontracted.
- The annual energy use of the legacy compressed air system was 9,925,573 kWh.
- The new Kaeser system is now 8,736,072, reducing the plant’s electricity consumption by 1,189,500 kWh.
- Specific power was reduced from 19.99 kW/100 cfm to 17.61 kW/100 cfm.
- Air solutions used all of its Save on Energy experience in applying for, and successfully winning a $183,000 Save on Energy compressor retrofit incentive for the company.
- Because the new Kaeser air compressors are air cooled, a further grant was secured for the supply and installation of hot air discharge ductwork. In summer, we direct unwanted heat outside the building. In winter, the hot air is forced into the adjacent manufacturing workspaces to create 116,000 m3/yr space heating.
Huge savings & incentives
This system overhaul has netted this client an impressive $154,635 in annual energy savings.
Maintenance costs have been reduced by an additional $46,000 per year and the Kaeser compressors include a five-year “bumper-to-bumper” warranty. This means that all unexpected, compressed-air-related repair costs are no longer a concern. In addition to these savings, Air solutions Canada helped to secure $196,000 in incentives, with $183,000 coming from Save on Energy and $13,000 from Enbridge Gas.
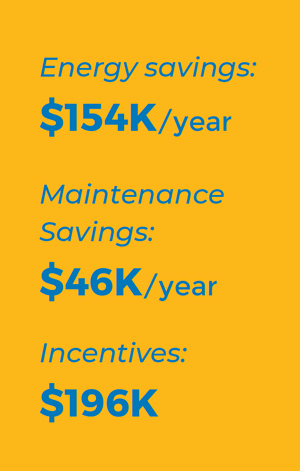
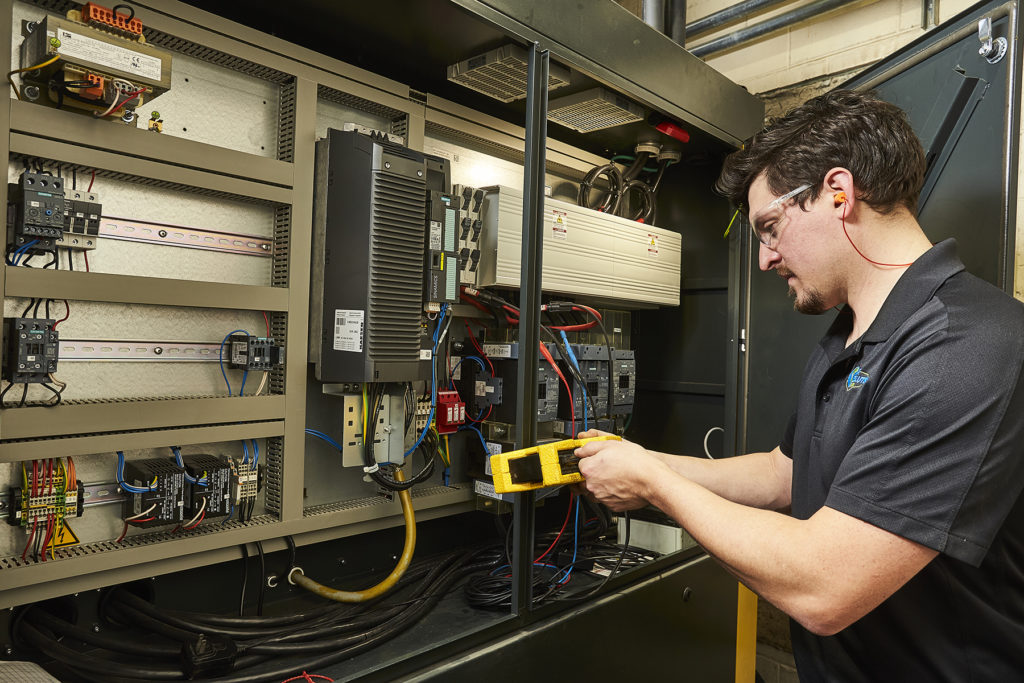
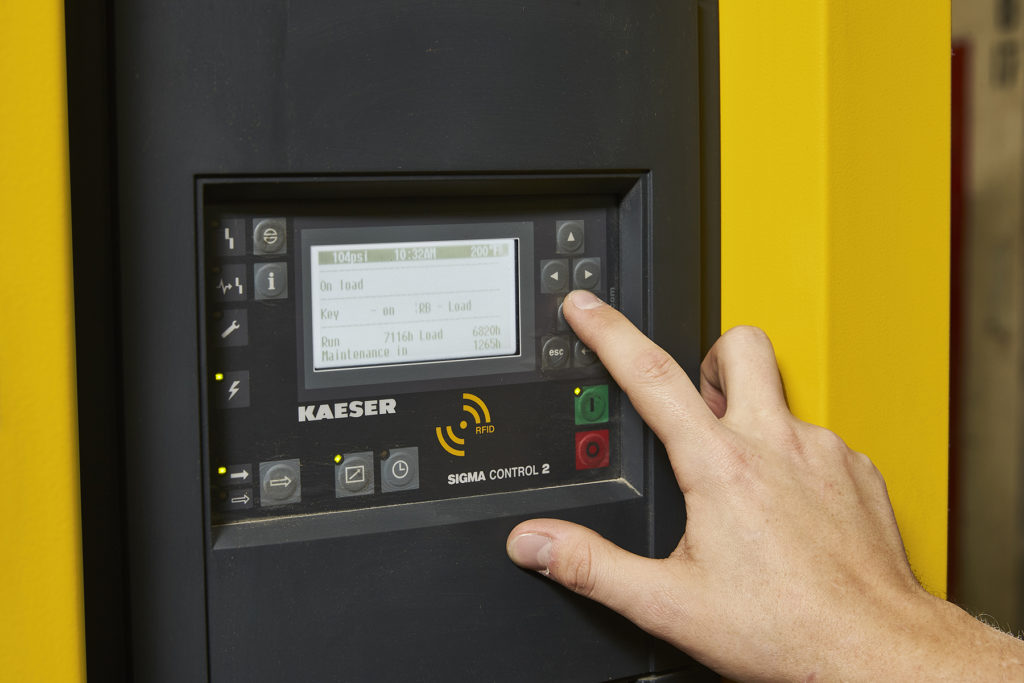
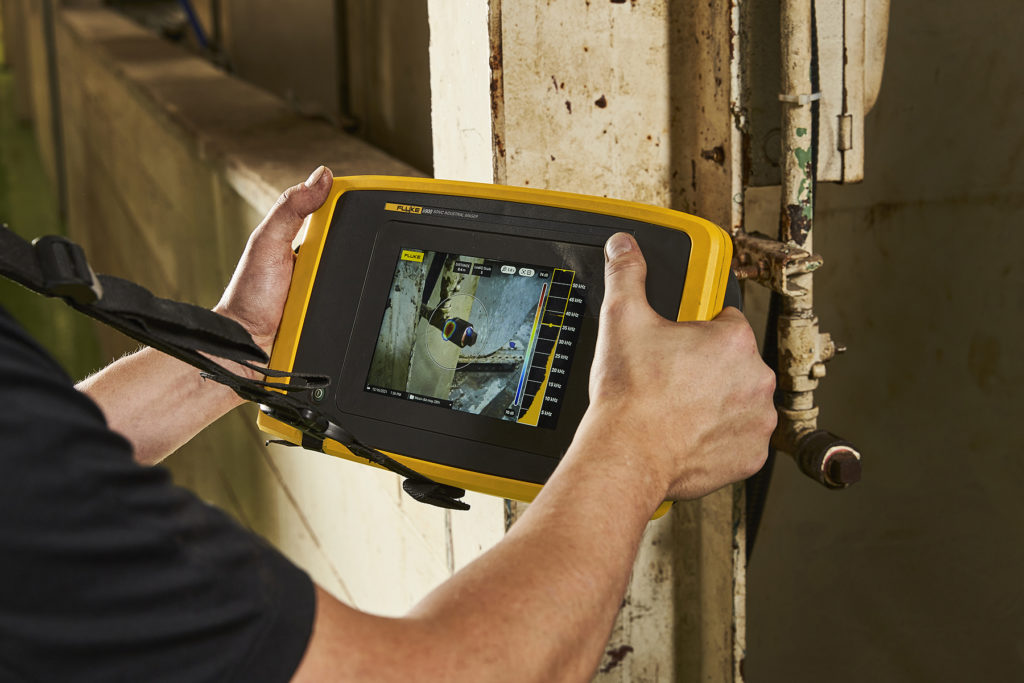
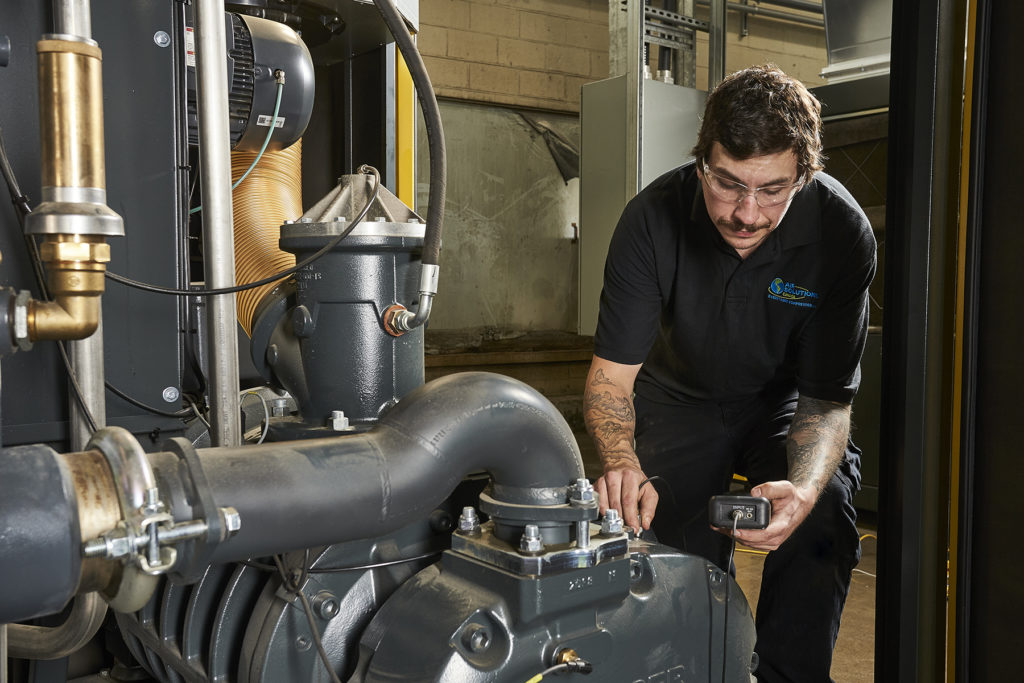
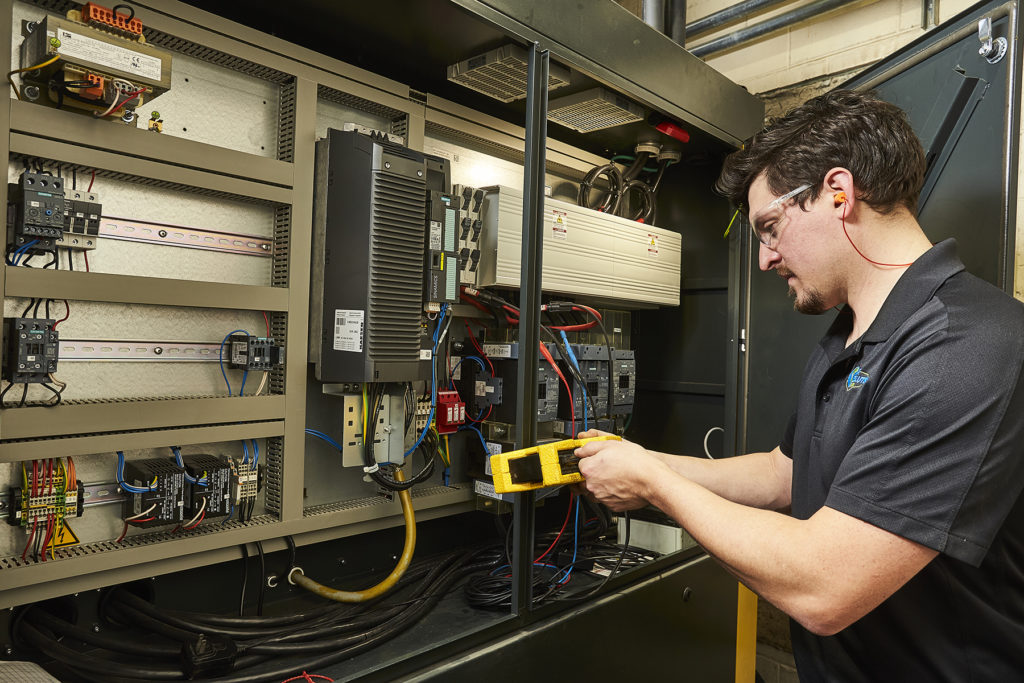
AS 13811
Discover your opportunities for savings!
Contact Air Solutions Canada to arrange your own comprehensive Air Demand Analysis, or a complimentary leak detection demonstration.
Just give us a call at 289-902-3576 or use the form above to get in touch.
Related products
The ultimate guide on rightsizing your compressed air system
Choosing the right compressed air system is crucial to minimize the total cost of ownership. How do you calculate the air demand in flow rate (CFM) and pressure (PSIG), what's the power requirement (V), and how does that translate in a compressed air system with one or more compressors (hp)?
Download our Comprehensive Guide for Choosing the Right Compressor Size!